Verification of a Relaxation Test with Visco Extended Drucker-Prager Model
Context
In this example, we simulate a relaxation test with a Visco Extended Drucker-Prager solid. This problem is solved using a viscoplastic solver (see Model: Viscoplasticity) in GEOS to predict the time-dependent deformation of the sample when subject to loading conditions. We verify the numerical results obtained by GEOS against a semi-analytical solution (see Visco Extended Drucker-Prager Model: Triaxial Driver versus Semi-Analytical Solution).
Input file
The xml input files for the test case are located at:
inputFiles/solidMechanics/viscoExtendedDruckerPrager_relaxation_base.xml
inputFiles/solidMechanics/viscoExtendedDruckerPrager_relaxation_benchmark.xml
A Python script for post-processing the simulation results is provided:
src/docs/sphinx/advancedExamples/validationStudies/viscoplasticity/RelaxationTest/relaxationTestFigure.py
Description of the case
We model the mechanical response of a viscoplastic slab subject to a displacement-controlled uniaxial loading and a constant confining stress, as shown below. The domain is homogeneous, isotropic, and isothermal. Before loading, the domain is initialized with isotropic stresses. Longitudinal compression is induced and governed by the normal displacement applied uniformly over the top surface. This compressive displacement is initially elevated to allow plastic hardening and then kept as a constant to mimic stress relaxation tests. In this example, fluid flow is not considered.

Fig. 75 Sketch of the problem
We set up and solve a Visco Extended Drucker-Prager model to obtain the spatial and temporal solutions of stresses and displacements across the domain upon loading. These numerical predictions are compared with the corresponding semi-analytical solutions derived from Runesson et al. (1999) (see Visco Extended Drucker-Prager Model: Triaxial Driver versus Semi-Analytical Solution).
For this example, we focus on the Mesh
,
the Constitutive
, and the FieldSpecifications
tags.
Mesh
The following figure shows the mesh used for solving this mechanical problem:
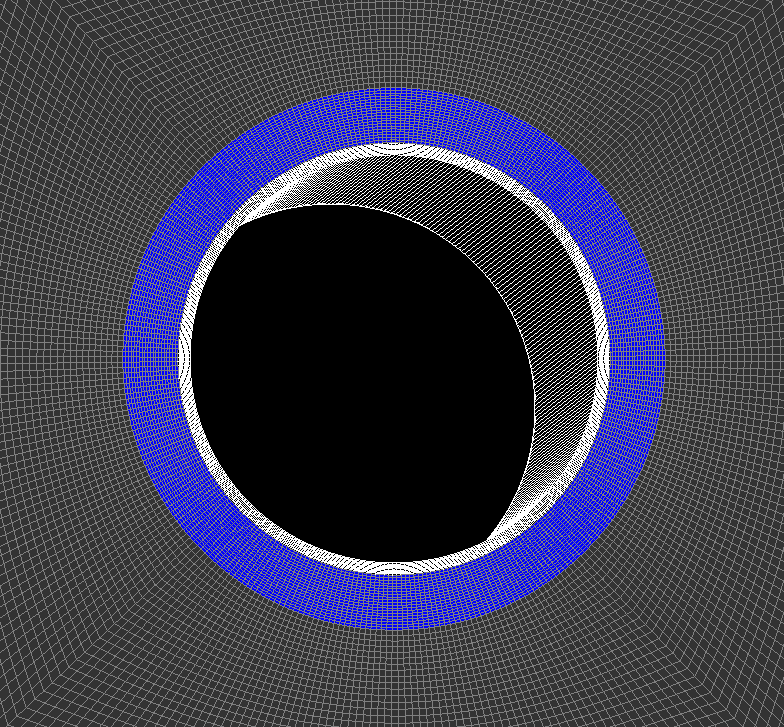
Fig. 76 Generated mesh
The mesh was created with the internal mesh generator and parametrized in the InternalMesh
XML tag.
It contains 10x10x10 eight-node brick elements in the x, y, and z directions respectively.
Such eight-node hexahedral elements are defined as C3D8
elementTypes, and their collection forms a mesh
with one group of cell blocks named here cellBlockNames
.
<Mesh>
<InternalMesh
name="mesh"
elementTypes="{ C3D8 }"
xCoords="{ 0, 0.9, 1.0 }"
yCoords="{ 0, 0.9, 1.0 }"
zCoords="{ 0, 0.9, 1.0 }"
nx="{ 9, 1 }"
ny="{ 9, 1 }"
nz="{ 9, 1 }"
cellBlockNames="{ cb-0_0_0, cb-1_0_0, cb-0_1_0, cb-1_1_0,
cb-0_0_1, cb-1_0_1, cb-0_1_1, cb-1_1_1 }"/>
</Mesh>
Solid mechanics solver
For the relaxation tests, pore pressure variations are neglected and subtracted from the analysis. Therefore, we define a solid mechanics solver, called here mechanicsSolver
.
This solid mechanics solver (see Solid Mechanics Solver) is based on the Lagrangian finite element formulation.
The problem is run as QuasiStatic
without considering inertial effects.
The computational domain is discretized by FE1
, defined in the NumericalMethods
section.
We use the targetRegions
attribute to define the regions where the solid mechanics solver is applied.
Here, we only simulate mechanical deformation in one region named as Domain
, whose mechanical properties are specified in the Constitutive
section.
<Solvers
gravityVector="{ 0.0, 0.0, 0.0 }">
<SolidMechanicsLagrangianFEM
name="mechanicsSolver"
logLevel="1"
discretization="FE1"
targetRegions="{ Domain }">
<NonlinearSolverParameters
newtonTol="1.0e-5"
newtonMaxIter="15"/>
<LinearSolverParameters
solverType="direct"/>
</SolidMechanicsLagrangianFEM>
</Solvers>
Constitutive laws
A homogeneous domain with one solid material is assumed, and its mechanical properties are specified in the Constitutive
section:
<Constitutive>
<ViscoExtendedDruckerPrager
name="rock"
defaultDensity="2700"
defaultBulkModulus="10.0e9"
defaultShearModulus="6.0e9"
defaultCohesion="0.1e6"
defaultInitialFrictionAngle="15.0"
defaultResidualFrictionAngle="20.0"
defaultDilationRatio="0.5"
defaultHardening="0.0005"
relaxationTime="5000.0"
/>
</Constitutive>
Recall that in the SolidMechanicsLagrangianFEM
section,
rock
is designated as the material in the computational domain.
Here, Visco Extended Drucker Prager model ViscoExtendedDruckerPrager
is used to simulate the viscoplastic behavior of rock
.
As for the material parameters, defaultInitialFrictionAngle
, defaultResidualFrictionAngle
and defaultCohesion
denote the initial friction angle, the residual friction angle, and cohesion, respectively, as defined by the Mohr-Coulomb failure envelope. As the residual friction angle defaultResidualFrictionAngle
is larger than the initial one defaultInitialFrictionAngle
, a strain hardening model is adopted, with a hardening rate given as defaultHardening="0.0005"
.
Finally, relaxationTime
is a key parameter for characterizing the viscoplastic behavior of the solid called rock
.
Constitutive parameters such as density, bulk modulus, and shear modulus are specified in the International System of Units.
Time history function
In the Tasks
section, PackCollection
tasks are defined to collect time history information from several property fields (time-series).
We can collect either the entire collection of field properties or specified named sets.
In this example, stressCollection
is specified to output the time history of stresses fieldName="rock_stress
for the selected subdomain objectPath="ElementRegions/Domain/cb8"
.
And displacementCollection
is defined to output the time history of displacement fieldName="totalDisplacement"
for the subset setNames="{ topPoint }"
.
<Tasks>
<PackCollection
name="stressCollection"
objectPath="ElementRegions/Domain/cb-1_1_1"
fieldName="rock_stress"/>
<PackCollection
name="displacementCollection"
objectPath="nodeManager"
fieldName="totalDisplacement"
setNames="{ topPoint }"/>
</Tasks>
These two tasks are triggered using the Event
management where PeriodicEvent
are defined for these recurring tasks.
GEOS writes two files named after the string defined in the filename
keyword and formatted as HDF5 files (displacement_history.hdf5 and stress_history.hdf5). The TimeHistory file contains the collected time history information from each specified time history collector. This information includes datasets for the simulation time, element center or nodal position, and the time history information.
We use a Python script to read and plot any specified subset of the time history data for verification and visualization.
Initial and boundary conditions
The next step is to specify fields, including:
The initial value (the stresses have to be initialized),
The boundary conditions (the displacement control, lateral confining stress, and constraints of the outer boundaries have to be set).
In this example, we specify isotropic stresses ( = -10.0 MPa,
= -10.0 MPa, and
= -10.0 MPa,).
A compressive traction ( = -10.0 MPa) is applied on the domain laterals
xpos
(all faces on the x-side of the domain, positive side) and ypos
(all faces on the y-side of the domain, positive side).
The normal displacement (axialload
) is instantaneously applied at the top surface zpos
(all surfaces on the top) at time = 0 s, and will gradually increase to a higher absolute value (-0.001) in 0.5 days to let the rock slab contract. Then, it remains constant for 1.5 days to allow stress relaxation.
The remaining outer boundaries of the domain are subjected to roller constraints.
These boundary conditions are set up through the FieldSpecifications
section.
The lateral traction and compressive displacement have negative values due to the negative sign convention for compressive stresses in GEOS.
<FieldSpecifications>
<FieldSpecification
name="xconstraint"
objectPath="nodeManager"
fieldName="totalDisplacement"
component="0"
scale="0.0"
setNames="{ xneg }"/>
<FieldSpecification
name="yconstraint"
objectPath="nodeManager"
fieldName="totalDisplacement"
component="1"
scale="0.0"
setNames="{ yneg }"/>
<FieldSpecification
name="zconstraint"
objectPath="nodeManager"
fieldName="totalDisplacement"
component="2"
scale="0.0"
setNames="{ zneg }"/>
<FieldSpecification
name="stressXX"
initialCondition="1"
setNames="{all}"
objectPath="ElementRegions/Domain"
fieldName="rock_stress"
component="0"
scale="-10.0e6"
/>
<FieldSpecification
name="stressYY"
initialCondition="1"
setNames="{all}"
objectPath="ElementRegions/Domain"
fieldName="rock_stress"
component="1"
scale="-10.0e6"
/>
<FieldSpecification
name="stressZZ"
initialCondition="1"
setNames="{all}"
objectPath="ElementRegions/Domain"
fieldName="rock_stress"
component="2"
scale="-10.0e6"
/>
<Traction
name="xconfinement"
setNames="{ xpos }"
objectPath="faceManager"
scale="-10.0e6"
tractionType="normal"
/>
<Traction
name="yconfinement"
setNames="{ ypos }"
objectPath="faceManager"
scale="-10.0e6"
tractionType="normal"
/>
<FieldSpecification
name="axialload"
objectPath="nodeManager"
fieldName="totalDisplacement"
component="2"
scale="-0.001"
functionName="timeFunction"
setNames="{ zpos }"/>
</FieldSpecifications>
The parameters used in the simulation are summarized in the following table.
Symbol |
Parameter |
Unit |
Value |
---|---|---|---|
Bulk modulus |
[GPa] |
10.0 |
|
Shear Modulus |
[GPa] |
6.0 |
|
Cohesion |
[MPa] |
0.1 |
|
Initial Friction Angle |
[degree] |
15.0 |
|
Residual Friction Angle |
[degree] |
20.0 |
|
Hardening Rate |
[-] |
0.0005 |
|
Relaxation Time |
[s] |
5000.0 |
|
Horizontal Stress |
[MPa] |
-10.0 |
|
Vertical Stress |
[MPa] |
-10.0 |
|
Traction at lateral |
[MPa] |
-10.0 |
Inspecting results
In the example, we request hdf5 output files for time-series (time history). We use Python scripts to visualize the outcome. The following figure shows the final distribution of vertical displacement upon loading.
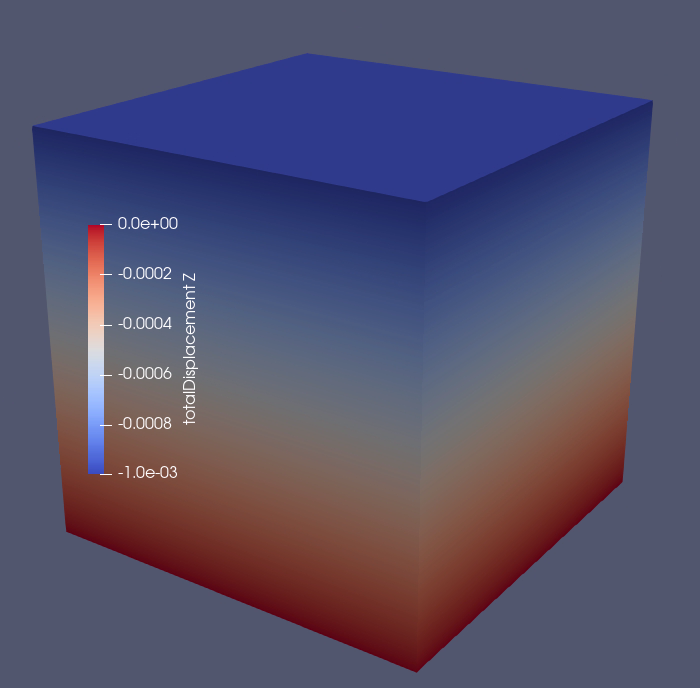
Fig. 77 Simulation result of vertical displacement
The figure below shows the comparisons between the numerical predictions (marks) and the corresponding analytical solutions (lines) with respect to stress–strain relationship, stress path on the top surface, the evolution of axial stress. Predictions computed by GEOS match the semi-analytical results. The bottom figure highlights the change in axial stress with time. Note that, if normal displacement remains constant, the axial stress decreases gradually to a residue value. This behavior is typically reported in the relaxation tests in laboratory.
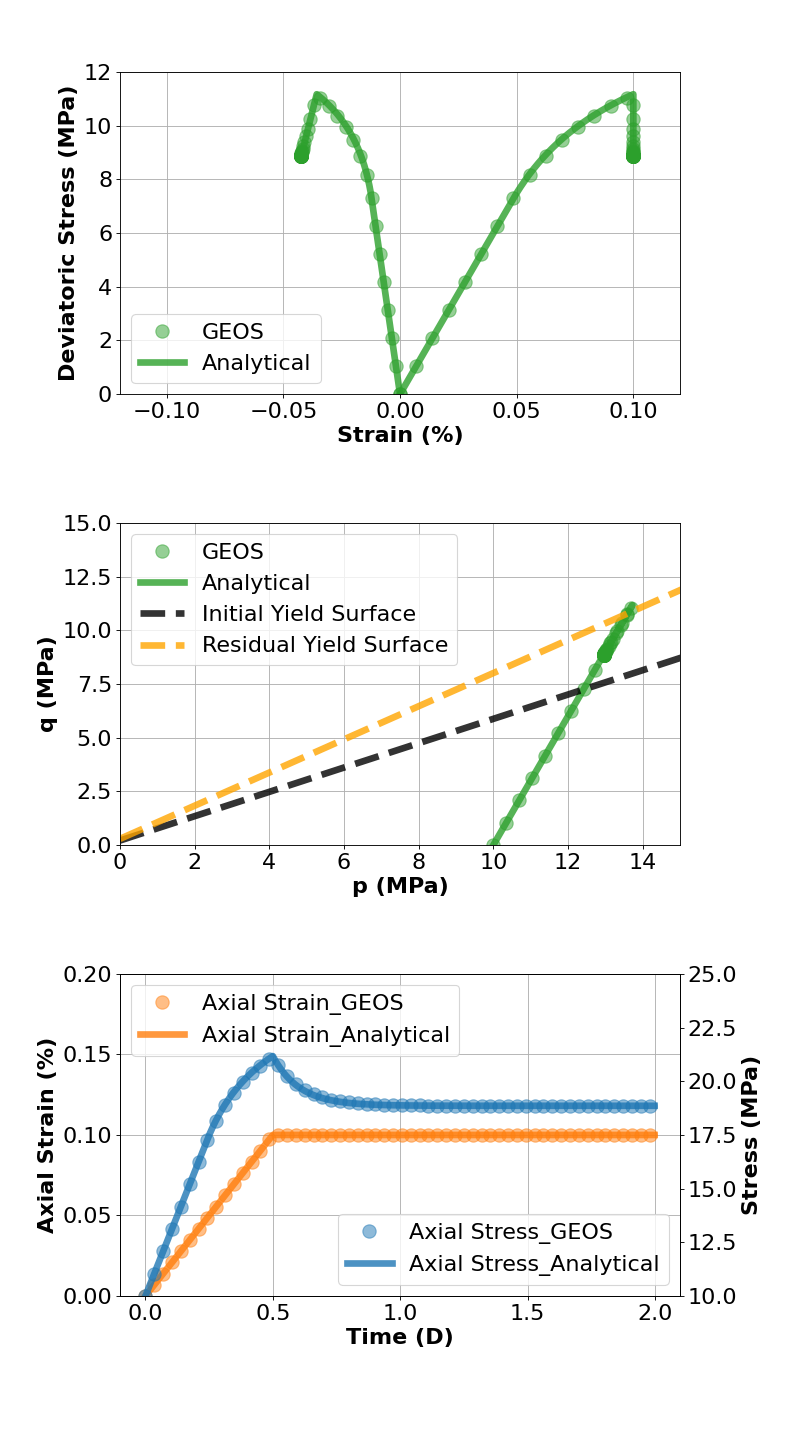
To go further
Feedback on this example
For any feedback on this example, please submit a GitHub issue on the project’s GitHub page.