CO2 Plume Evolution With Hysteresis Effect on Relative Permeability
Context
We consider a benchmark problem used in (Class et al., 2009) to compare a number of numerical models applied to CO2 storage in geological formations. Using a simplified miscible two-phase setup, this test case illustrates the modeling of solubility trapping (with CO2 dissolution in brine) and residual trapping (with gas relative permeability hysteresis) in CO2-brine systems.
Our goal is to review the different sections of the XML file reproducing the benchmark configuration and to demonstrate that the GEOS results (i.e., mass of CO2 dissolved and mobile for both hysteretic and non-hysteretic configurations) are in agreement with the reference results published in (Class et al., 2009) Problems 3.1 and 3.2.
Input file
This benchmark test is based on the XML file located below:
../../../../../../../inputFiles/compositionalMultiphaseWell/benchmarks/Class09Pb3/class09_pb3_smoke_3d.xml
../../../../../../../inputFiles/compositionalMultiphaseWell/benchmarks/Class09Pb3/class09_pb3_drainageOnly_iterative_base.xml
Problem description
The following text is adapted from the detailed description of the benchmark test case presented in (Class et al., 2009).
The setup is illustrated in the figure below. The mesh can be found in GEOSDATA and was provided for the benchmark. It discretizes the widely-used Johansen reservoir, which consists in a tilted reservoir with a main fault. The model domain has the following dimensions: 9600 x 8900 x [90-140] m. Both porosity and permeability are heterogeneous and given at vertices. A single CO2 injection well is located at (x,y) = (5440,3300) m with perforations only in the bottom 50 m of the reservoir. The injection takes place during the first 25 years of the 50-year simulation at the constant rate of 15 kg/s. A hydrostatic pressure gradient is imposed on the boundary faces as well as a constant geothermal gradient of 0.03 K/m.
The authors have used the following simplifying assumptions:
The formation is isotropic.
The temperature is constant in time.
The pressure conditions at the lateral boundaries are constant over time, and equal to the initial hydrostatic condition.
Mesh and element regions
The proposed conforming discretization is fully hexahedral.
A VTK filter PointToCell
is used to map properties from vertices to cells, which by default builds a uniform average of
values over the cell.
The structured mesh is generated using some helpers python scripts from the formatted Point/Cells list provided.
It is then imported using meshImport
<Mesh>
<InternalMesh
name="mesh1"
elementTypes="{ C3D8 }"
xCoords="{ 5240, 5640 }"
yCoords="{ 3100, 3500 }"
zCoords="{ -3000, -2950 }"
nx="{ 5 }"
ny="{ 5 }"
nz="{ 5 }"
cellBlockNames="{ 1_hexahedra }">
<InternalWell
name="wellInjector1"
wellRegionName="wellRegion"
wellControlsName="wellControls"
logLevel="1"
polylineNodeCoords="{ { 5440.0, 3300.0, -2950.0 },
{ 5440.0, 3300.0, -3000.00 } }"
polylineSegmentConn="{ { 0, 1 } }"
radius="0.1"
numElementsPerSegment="5">
<Perforation
name="injector1_perf1"
distanceFromHead="45"/>
<Perforation
name="injector1_perf2"
distanceFromHead="35"/>
<Perforation
name="injector1_perf3"
distanceFromHead="25"/>
<Perforation
name="injector1_perf4"
distanceFromHead="15"/>
<Perforation
name="injector1_perf5"
distanceFromHead="5"/>
</InternalWell>
</InternalMesh>
</Mesh>
The central wellbore is discretized internally by GEOS (see CO 2 Injection).
It includes five segments with a perforation in each segment. It has its own region wellRegion
and control labeled wellControls
defined and detailed respectively in ElementRegions and Solvers (see below).
In the ElementRegions block,
<ElementRegions>
<CellElementRegion
name="reservoir"
cellBlocks="{ * }"
materialList="{ fluid, rock, relperm, cappres }"/>
<WellElementRegion
name="wellRegion"
materialList="{ fluid }"/>
</ElementRegions>
one single reservoir region labeled reservoir
.
A second region wellRegion
is associated with the well.
All those regions define materials to be specified inside the Constitutive block.
Coupled solver
The simulation is performed by the GEOS coupled solver for multiphase flow and well defined in the XML block CompositionalMultiphaseReservoir:
<CompositionalMultiphaseFVM
name="compositionalMultiphaseFlow"
targetRegions="{ reservoir }"
discretization="fluidTPFA"
temperature="363"
maxCompFractionChange="0.2"
logLevel="1"
useMass="1"/>
It references the two coupled solvers under the tags flowSolverName
and wellSolverName
. These are defined inside the same Solvers block
following this coupled solver. It also defined non-linear, NonlinearSolverParameters and
and linear, LinearSolverParameters, strategies.
The next two blocks are used to define our two coupled physics solvers compositionalMultiphaseFlow
(of type CompositionalMultiphaseFVM)
and compositionalMultiphaseWell
(of type CompositionalMultiphaseWell).
Flow solver
We use the targetRegions
attribute to define the regions where the flow solver is applied.
<CompositionalMultiphaseReservoir
name="coupledFlowAndWells"
flowSolverName="compositionalMultiphaseFlow"
wellSolverName="compositionalMultiphaseWell"
logLevel="1"
initialDt="1e2"
targetRegions="{ reservoir, wellRegion }">
<NonlinearSolverParameters
newtonTol="1.0e-5"
newtonMaxIter="40"/>
<LinearSolverParameters
solverType="fgmres"
preconditionerType="mgr"
krylovTol="1e-6"
logLevel="1"/>
</CompositionalMultiphaseReservoir>
The FV scheme discretization used is TPFA (which definition can be found nested in NumericalMethods/FiniteVolume) and some parameter values.
Well solver
The well solver is applied on its own region wellRegion
which consists of the five discretized segments.
It is also the place where the WellControls are set thanks to type
, control
, injectionStream
,
injectionTemperature
, targetTotalRateTableName
and, targetBHP
for instance if we consider an injection well.
For more details on the wellbore modeling please refer to Compositional Multiphase Well Solver.
<CompositionalMultiphaseWell
name="compositionalMultiphaseWell"
targetRegions="{ wellRegion }"
logLevel="1"
useMass="1">
<WellControls
name="wellControls"
logLevel="1"
type="injector"
control="totalVolRate"
referenceElevation="-3000"
targetBHP="1e8"
enableCrossflow="0"
useSurfaceConditions="1"
surfacePressure="101325"
surfaceTemperature="288.71"
targetTotalRateTableName="totalRateTable"
injectionTemperature="353.15"
injectionStream="{ 1.0, 0.0 }"/>
<WellControls
name="MAX_MASS_INJ"
logLevel="1"
type="injector"
control="massRate"
referenceElevation="-3000"
targetBHP="1e8"
enableCrossflow="0"
useSurfaceConditions="1"
surfacePressure="101325"
surfaceTemperature="288.71"
targetMassRate="15"
injectionTemperature="353.15"
injectionStream="{ 1.0, 0.0 }"/>
<WellControls
name="MAX_MASS_INJ_TABLE"
logLevel="1"
type="injector"
control="massRate"
referenceElevation="-3000"
targetBHP="1e8"
enableCrossflow="0"
useSurfaceConditions="1"
surfacePressure="101325"
surfaceTemperature="288.71"
targetMassRateTableName="totalMassTable"
injectionTemperature="353.15"
injectionStream="{ 1.0, 0.0 }"/>
</CompositionalMultiphaseWell>
Constitutive laws
This benchmark test involves a compositional mixture that defines two phases (CO2-rich and aqueous) labeled as
gas
and water
which contain two components co2
and water
. The miscibility of CO2 results in the
presence of CO2 in the aqueous phase. The vaporization of H2O in the CO2-rich phase is not considered here.
<CO2BrineEzrokhiFluid
name="fluid"
phaseNames="{ gas, water }"
componentNames="{ co2, water }"
componentMolarWeight="{ 44e-3, 18e-3 }"
phasePVTParaFiles="{ tables/pvtgas.txt, tables/pvtliquid_ez.txt }"
flashModelParaFile="tables/co2flash.txt"/>
The brine properties are modeled using Ezrokhi correlation, hence the block name CO2BrineEzrokhiFluid. The external PVT files tables/pvtgas.txt and tables/pvtliquid_ex.txt give access to the models considered respectively for the computation of gas density and viscosity and the brine density and viscosity, along with pressure, temperature, salinity discretization of the parameter space. The external file tables/co2flash.txt gives the same type of information for the CO2Solubility model (see CO2-brine model for details).
The rock model defines a slightly compressible porous medium with a reference porosity equal to 0.1.
<CompressibleSolidConstantPermeability
name="rock"
solidModelName="nullSolid"
porosityModelName="rockPorosity"
permeabilityModelName="rockPerm"/>
<NullModel
name="nullSolid"/>
<PressurePorosity
name="rockPorosity"
defaultReferencePorosity="0.1"
referencePressure="1.0e7"
compressibility="4.5e-10"/>
<ConstantPermeability
name="rockPerm"
permeabilityComponents="{ 1.0e-12, 1.0e-12, 1.0e-12 }"/>
The relative permeability model is input through tables thanks to TableRelativePermeability block.
<TableRelativePermeability
name="relperm"
phaseNames="{ gas, water }"
wettingNonWettingRelPermTableNames="{ waterRelativePermeabilityTable,
gasRelativePermeabilityTable }"/>
As this benchmark is testing the sensitivity of the plume dynamics to the relative permeability hysteresis modeling,
in commented block the TableRelativePermeabilityHysteresis block sets up bounding curves for imbibition and drainage
under imbibitionNonWettingRelPermTableName
, imbibitionWettingRelPermTableName
and, drainageWettingNonWettingRelPermTableNames
compared to the wettingNonWettingRelPermTableNames
label of the drainage only TableRelativePermeability blocks.
Those link to TableFunction blocks in Functions, which define sample points for piecewise linear interpolation.
This feature is used and explained in more details in the following section dedicated to Initial and Boundary conditions.
See,
../../../../../../../inputFiles/compositionalMultiphaseWell/benchmarks/Class09Pb3/class09_pb3_hystRelperm_iterative_base.xml
for the input base with relative permeability hysteresis setup.
<TableRelativePermeabilityHysteresis
name="relperm"
phaseNames="{ gas, water }"
drainageWettingNonWettingRelPermTableNames="{ drainageWaterRelativePermeabilityTable,
drainageGasRelativePermeabilityTable }"
imbibitionNonWettingRelPermTableName="imbibitionGasRelativePermeabilityTable"
imbibitionWettingRelPermTableName="imbibitionWaterRelativePermeabilityTable"/>
Note
wettingNonWettingRelPermTableNames
in TableRelativePermeability and drainageWettingNonWettingRelPermTableNames
in
TableRelativePermeabilityHysteresis are identical.
Capillary pressure is also tabulated and defined in TableCapillaryPressure. No hysteresis is modeled yet on the capillary pressure.
<TableCapillaryPressure
name="cappres"
phaseNames="{ gas, water }"
wettingNonWettingCapPressureTableName="waterCapillaryPressureTable"/>
Initial and boundary conditions
The domain is initially saturated with brine with a hydrostatic pressure field. This is specified using the HydrostaticEquilibrium XML tag in the FieldSpecifications block. The datum pressure and elevation used below are defined in (Class et al., 2009)).
<HydrostaticEquilibrium
name="equil"
objectPath="ElementRegions"
datumElevation="-3000"
datumPressure="3.0e7"
initialPhaseName="water"
componentNames="{ co2, water }"
componentFractionVsElevationTableNames="{ initCO2CompFracTable,
initWaterCompFracTable }"
temperatureVsElevationTableName="initTempTable"/>
In the Functions block, the TableFunction s named initCO2CompFracTable
and initWaterCompFracTable
define the brine-saturated initial state, while the TableFunction named initTempTable
defines the temperature field as a function of depth to impose the geothermal gradient.
The boundaries are set to have a constant 0.03 K/m temperature gradient as well as the hydrostatic pressure gradient.
We supplement that with water dominant content. Each block is linking a fieldName
to a TableFunction tagged as
the value of functionName
. In order to have those imposed on the boundary faces, we provide faceManager
as objectPath
.
<FieldSpecification
name="bcPressure"
objectPath="faceManager"
setNames="{3}"
fieldName="pressure"
functionName="pressureFunction"
scale="1"/>
<FieldSpecification
name="bcTemperature"
objectPath="faceManager"
setNames="{3}"
fieldName="temperature"
functionName="temperatureFunction"
scale="1"/>
<FieldSpecification
name="bcCompositionCO2"
objectPath="faceManager"
setNames="{3}"
fieldName="globalCompFraction"
component="0"
scale="0.000001"/>
<FieldSpecification
name="bcCompositionWater"
objectPath="faceManager"
setNames="{3}"
fieldName="globalCompFraction"
component="1"
scale="0.999999"/>
Outputing reservoir statistics
In order to output partitioning of CO2 mass, we use reservoir statistics implemented in GEOS. This is done by defining a Task, with
flowSolverName
pointing to the dedicated solver and computeRegionStatistics
set to 1 to compute statistics by regions.
The setNames
field is set to 3 as it is its attribute tag in the input vtu mesh.
<CompositionalMultiphaseStatistics
name="compflowStatistics"
flowSolverName="compositionalMultiphaseFlow"
logLevel="1"
computeCFLNumbers="1"
computeRegionStatistics="1"/>
and an Event for this to occur recursively with a forceDt argument for the period over which statistics are output and target pointing towards the aforementioned Task.
<PeriodicEvent
name="statistics"
timeFrequency="1e5"
target="/Tasks/compflowStatistics"/>
This is a sample of the output we will have in the log file.
compflowStatistics, reservoir: Pressure (min, average, max): 2.5139e+07, 2.93668e+07, 3.23145e+07 Pa
compflowStatistics, reservoir: Delta pressure (min, max): -12157, 158134 Pa
compflowStatistics, reservoir: Temperature (min, average, max): 293.15, 371.199, 379.828 K
compflowStatistics, reservoir: Total dynamic pore volume: 1.57994e+09 rm^3
compflowStatistics, reservoir: Phase dynamic pore volumes: { 1.00239e+06, 1.57894e+09 } rm^3
compflowStatistics, reservoir: Phase mass (including both trapped and non-trapped): { 7.24891e+08, 1.6245e+12 } kg
compflowStatistics, reservoir: Trapped phase mass: { 5.3075e+08, 3.2511e+11 } kg
compflowStatistics, reservoir: Dissolved component mass: { { 7.13794e+08, 4.53966e+06 }, { 1.6338e+08, 1.62433e+12 } } kg
compflowStatistics: Max phase CFL number: 65.1284
compflowStatistics: Max component CFL number: 2.32854
Note
The log file mentioned above could be an explicit printout of the stdio from MPI launch or the autogenerated output from a SLURM job slurm.out or similar
Inspecting results
We request VTK-format output files and use Paraview to visualize the results under the Outputs block.
The following figure shows the distribution of CO2 saturation thresholded above a significant value (here 0.001). The displayed cells are colored with respect to the CO2 mass they contain. If the relative permeability for the gas phase drops below 10e-7, the cell is displayed in black.
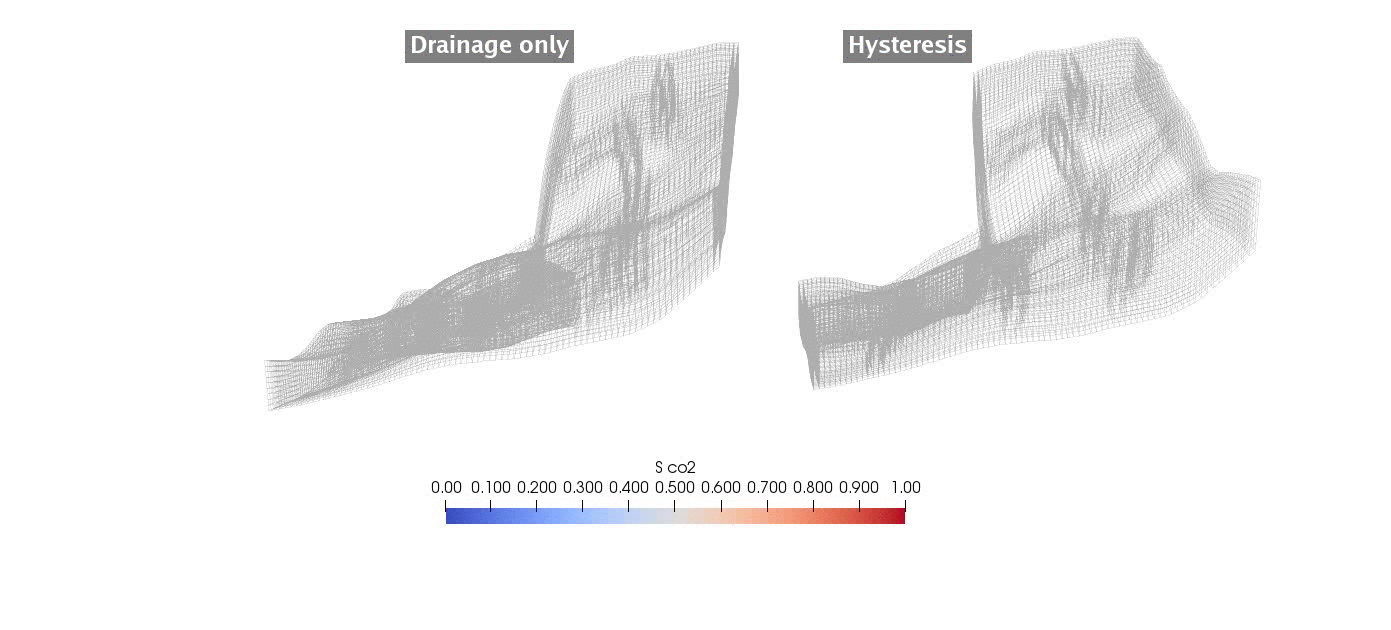
Fig. 13 Plume of CO2 saturation for significant value where immobile CO2 is colored in black.
We observe the importance of hysteresis modeling in CO2 plume migration. Indeed, during the migration phase, the cells at the tail of the plume are switching from drainage to imbibition and the residual CO2 is trapped. This results in a slower migration and expansion of the plume.
To validate the GEOS results, we consider the metrics used in (Class et al., 2009). The reporting values are the dissolved and gaseous CO2 with respect to time using only the drainage relative permeability and using hysteretic relative permeabilities.
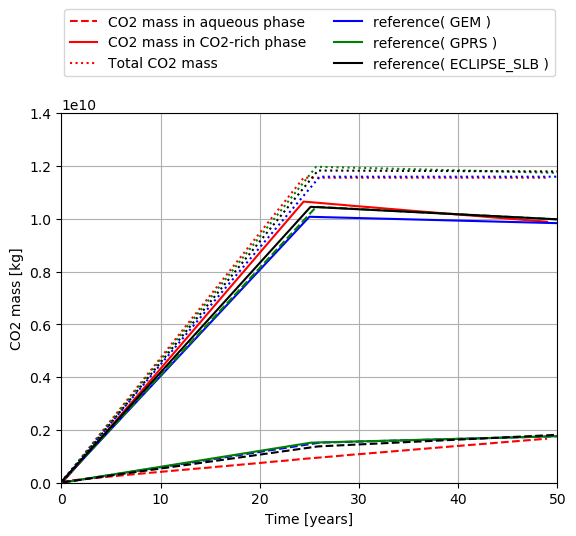
Fig. 14 CO2 mass in aqueous and CO2-rich phases as a function of without relative permeability hysteresis
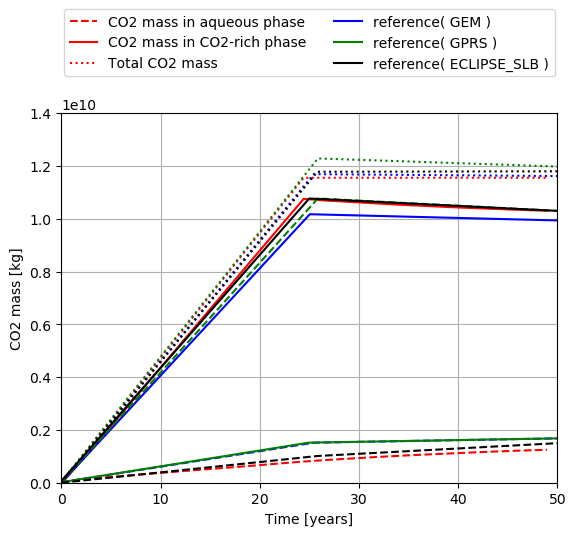
Fig. 15 CO2 mass in aqueous and CO2-rich phases as a function of time with relative permeability hysteresis
We can see that at the end of the injection period the mass of CO2 in the gaseous phase stops increasing and starts decreasing due to dissolution of CO2 in the brine phase. These curves confirm the agreement between GEOS and the results of (Class et al., 2009).
To go further
Feedback on this example
For any feedback on this example, please submit a GitHub issue on the project’s GitHub page.